Case Studies
Business Challenge:
A collaborator of USEA was recently observing an increased failure rate of a component and asked USEA to investigate the issue and identify the root cause.
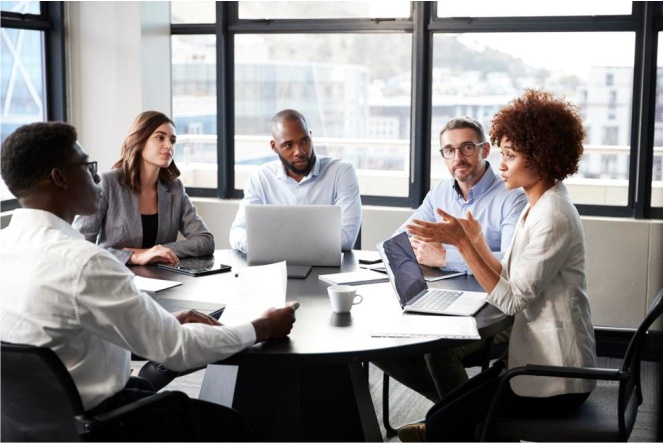
In Depth Failure Analysis:
The initial work done by USEA involved an industry standard 8D investigation to determine whether device fabrication or testing parameters had changed. Took an advanced investigation that included:
• Parametric data collection during temperature cycling, including a study to investigate whether parametric data drifted during the tests.
• CSAM analysis to determine whether there was a mechanical failure or delamination in the components.
• Finite Element Modeling (FEM) to investigate how defects in the component assembly could result in failure during temperature cycling.
These investigations did not reveal any increased failure rates for the component.
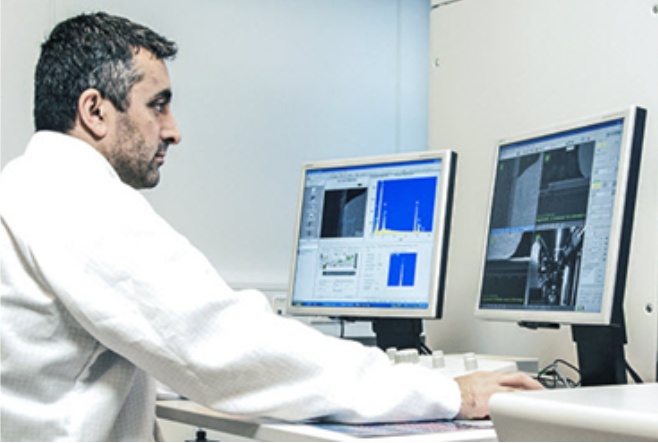
Downstream Analysis:
USEA also investigated what happened to the component after its release. Through detailed discussions with our collaborators and subcontractors, we learned that the component was mounted onto the device board at a subcontractor’s facility, subjected to temperature cycling tests, and then functionally tested. It was during this phase that the increased failure rates were observed.
Further analysis revealed that the subcontractor had changed the soldering process for mounting the components. They switched to RoHS-compliant solder, which required higher temperatures. Based on this information, we hypothesized that the increased failure rates were due to temperature-induced stress on the die during the soldering process.
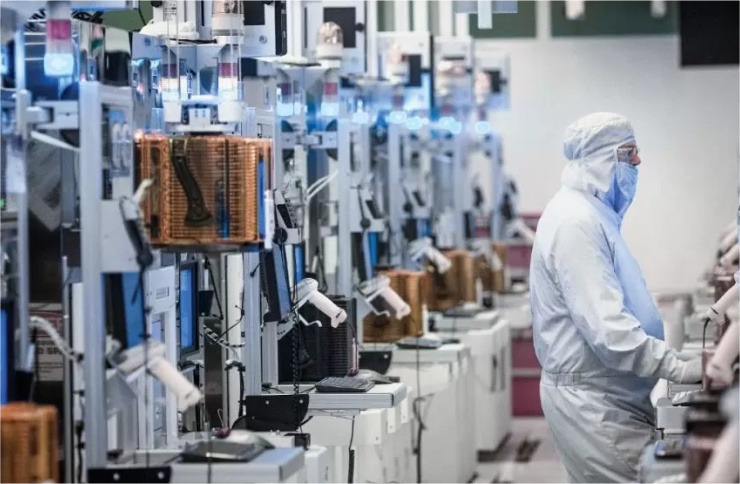